质量管理体系中的不符合项、产品和服务的不合格输出和产品缺陷都称为质量问题,而质量问题的处理是质量管理工作中经常面临的一项政策性、技术性、专业性很强的工作。随着质量管理工作规范性要求的提升,对质量问题处理的规范性要求也越来越高。为此,本文介绍质量问题“双归零处理方法以及难点研究,供业界参考和借鉴。质量问题“双归零的基本概念质量问题“双归零是指技术归零和管理归零,技术归零是指从技术上按 “定位准确、机理清楚、问题复现、措施有效、举一反三的五条要求逐条落实,形成技术归零报告或技术文件的活动。管理归零是指从管理上按 “过程清楚、责任明确、措施落实、严肃处理、完善规章的五条要求逐条落实,形成管理归零报告或相关文件的活动。其工作过程见下文“质量问题‘双归零’处理流程图。质量问题“双归零处理的难点质量问题的定性难质量问题通常按照偏离规定要求的严重程度和造成损失的大小分为3类,即重大质量问题、严重质量问题、通常质量问题。不符合项在质量管理体系中有通常不符合项和严重不符合项。缺陷分为轻微、严重和致命缺陷3类。由于定义都是定性的描述,没有明明确量标准,必须负责处理质量问题的人员具有丰富的工作经验。同时由于产品的规范和体系标准中不可能把质量问题可能出现的现象和模式全部列出来,因此导致质量问题定性难。质量问题的原因定位难无论是技术质量问题或管理质量问题还是产品缺陷,仅有明确了问题发生的根本原因才能对症下药,制定详细的改进措施。但实际工作中,由于质量问题第一表现形式为出现问题的结果,很少能直接判断出问题的直接原因,特别是原因的关键点,或可控的工艺、体系、过程等环节,因此,在处理过程中原因定位准确成为问题能否彻底解决的关键。质量问题故障复现难由于装备自身的特点,特别是一次性使用的装备,如弹药,大部分性能不易检测,仅有在完成功能后才能表现出来,不能通过测试、无损检测等手段完全模拟或重现出现问题的现象,导致故障很难复现。质量问题涉及范围界定难,消除产品存在的隐患困难通常情况下,由于生产方式的原因,质量问题大多在科研试验、生产过程、产品交验试验或使用的过程和服务中产生,因此,涉及的产品或体系都不是单件产品或单一要素,而是批量的产品,多个过程可能存在隐患。怎样找到合理的依据,明确质量问题涉及的范围,成为质量问题处理的落脚点,也是此项工作的难点。质量问题“双归零处理的对策按照质量问题归零处理的要求,关键在于针对存在的4个方面的难点采取相应的对策和措施。准确明确质量问题的性质和级别质量问题发生后,明确质量问题的性质和级别是处理质量问题的第1个关键点。在归零要求中,明确问题的性质和级别是必须尽快完成的一项基本要求,重点要注意以下3个方面的工作:一是区分缺陷和质量问题之间的关系。按照GJB 1405A-2006的定义,缺陷为未满足与预期或规定用途有关的要求。从缺陷的定义能够看出,在产品的制造与验收规范中,对于缺陷的分类已经基本明确,并与产品的抽样方案结合起来,依据产品使用情况,选定产品合格可接受质量水平,给出判定合格标准。致命缺陷通常与安全性有关,或导致产品性能存在重大缺陷。按照规范判定不容许有,因此,通常对照为重大质量问题,必须严格按照程序上报。严重缺陷通常与可靠性、维修性、配套性相关。在产品的抽样过程中,发现单位产品存在缺陷,特别是出现严重缺陷和轻缺陷时,按照规范的判定准则,不一定判定为批次产品不合格,因此,实际上我们接受的产品存在一定的没有超出规范判定标准约定的缺陷。存在严重缺陷但不一定按规范判定为批次不合格,因此,不是所有的严重缺陷对应为严重质量问题。在实际工作中,依据规范判定的结果,假如因严重缺陷导致批次产品不合格,通常定性为严重质量问题,并按照程序组织归零处理。同时,对于存在的严重缺陷尽管不构成批次不合格,但也应给予关注,并按照不合格品管理的程序要求,采用纠正或纠正措施,剔除缺陷产品。至于轻缺陷,通常指外观、非关键尺寸等存在不合格情况,通常不会导致产品性能的严重降低,尽管判定批次不合格,但采取措施能很快消除,通常按通常质量问题加以归零处理或者按照不合格品审理的程序来处理。二是处理好不合格输出与质量问题的关系。不合格定义:不符合合同、图纸、样件、技术条件或其他规定的技术文件的要求。不合格输出定义:任何具有1个或1个以上不符合合同、图纸、样件、技术条件或其他规定的技术文件的要求之特性的产品和服务。依据定义,不合格输出通常是指经过设计定型的产品,在生产、使用等过程中出现不合格。但从实际的执行工作来看,质量问题处理消除的是产品存在某种不合格或缺陷存在的状态,使其满足规范等技术文件的要求。而不合格输出处理则是指消除某个具体产品实际存在的不合格或缺陷的点。共同点是要求采取纠正措施消除不合格或缺陷。三是明确好质量问题的级别。对于质量问题级别,通常依据产品规范给出的判定标准,按前面的定义对质量问题级别给出明确判定。假如不能明确界定问题的级别,通常考虑按严重质量问题看待,并在后续的工作中进行修正。对于质量问题是属于技术问题还是管理问题,或者两种情况都存在,在分辨不清的情况下,通常按技术质量问题对待,并在后续的原因分析过程中进行明确。系统分析找出问题的主要原因无论是技术质量问题还是管理方面的质量问题,仅有明确了问题发生的关键原因,才能对症下药。这是质量问题处理的第2个关键点,核心内容在于明确产品出现问题的系统或产品部位。针对质量问题的具体情况,从产品的工程设计方面、生产控制方面、质量管理方面等进行全面分析,通常采用理论分析、调查试验、分析检查、与同类质量问题信息进行类比,按故障树要求采取排除法进行试验验证,对质量问题的每一项证据内容进行核实,分清是人为责任还是非人为责任,明确判断质量问题属于何种原因引起,推测问题现象的惟一性。对质量问题的定位要从上到下层层分解,逐步定位到单机、部件,直至零件、元器件、原资料或软件某一运行状态或某一特定接口,其通常要求包含:督促成立质量问题排查工作小组;运用PDCA法则,制定排查工作规划;采用故障模式影响分析(FMEA)和故障树分析法(FTA),建立故障树,制订质量问题分析试验大纲,采取排除法进行质量问题分析定位;利用观察、理化分析、解剖、X射线检查、电子扫描、测试、试验等方法对质量问题进行准明确位。采取措施力争实现故障再现技术质量问题处理原则上都应故障复现,这是质量问题处理的第3个关键点。技术质量问题复现通常要求包含:质量问题复现通常通过模拟试验,如静态检测试验、动态试验,验证质量问题定位的准确性和机理分析的正确性;对小概率事件也不能轻易放过,要进行充分的验证试验,证明产品的可靠性有保障的条件下,并经专家评审确认后续产品不会发生类似问题,才能放行;对于问题不能复现的,应进行问题原理性复现,即复现导致问题现象发生的模式。同时对该情况还应进行分析论证,在采取措施后,能够确保该问题不影响型式试验或后续产品质量,并经专家和相关部门认可。准确界定质量问题涉及的范围,消除产品和服务中存在的隐患由于生产方式的原因,产品发生问题时,往往已生产出一批或几批产品,涉及的数量大、范围广。怎样界定质量问题的范围和产品批次、数量,是解决质量问题最终取得实际效果的关键。假如解决质量问题的方法是改进设计时,还包含对产品图样、技术文件、技术状态的工程更改,以及明确是否必须对已交付的各类技术资料进行更改等。通常的程序和要求有以下几个方面:1. 制定纠正措施和实施计划为了消除隐患,避免同样问题重复发生,有关单位应制定具体可行的纠正措施和实施计划,在计划中有具体落实纠正措施的负责人和完成日期。2. 评审和确认纠正措施要通过一定试验至少是产品发生问题的试验来验证其有效性,同时应分析纠正措施实施的可行性,避免带来新的问题或其他不可靠因素,重大纠正措施应当组织同行业专家评审。3.实施纠正措施把经过评审和确认的纠正措施反馈到设计、工艺或试验和体系之中,通过技术状态管理程序和体系程序完成相应文件更改和产品更改。4. 纠正措施的记录与监督在纠正措施实施过程中,有关人员应做好实施纠正措施的完整的、可追溯性的记录。质量管理人员要对实施过程做好监督检查,必要时专业技术人员可采取模拟实际环境进行试验,对实施效果进行评审等手段来评价纠正措施的可行性和有效性,完成“归零工作。结语无论是技术归零还是管理归零,评审是完成“归零工作的1个重要环节。通过邀请专家评审,对质量问题的整个处理过程进行一次全面的梳理,提出完善可行的改进意见和建议,可为避免出现类似质量问题,尤其是防止同类质量问题的重复发生打下坚实的基础。
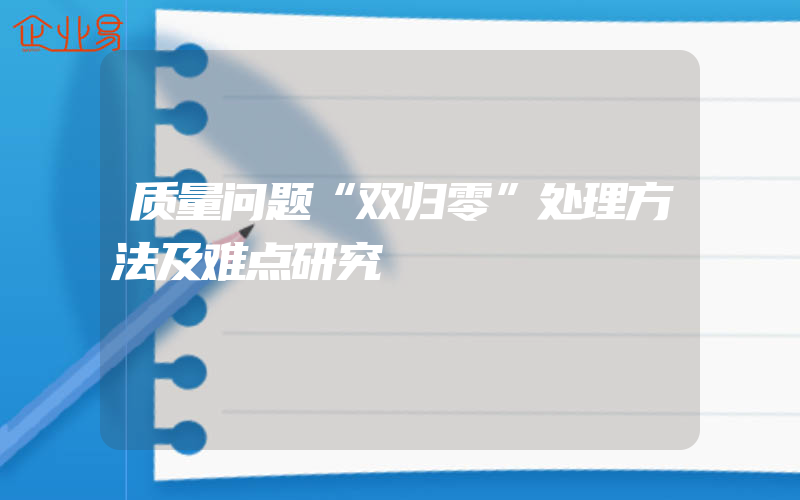